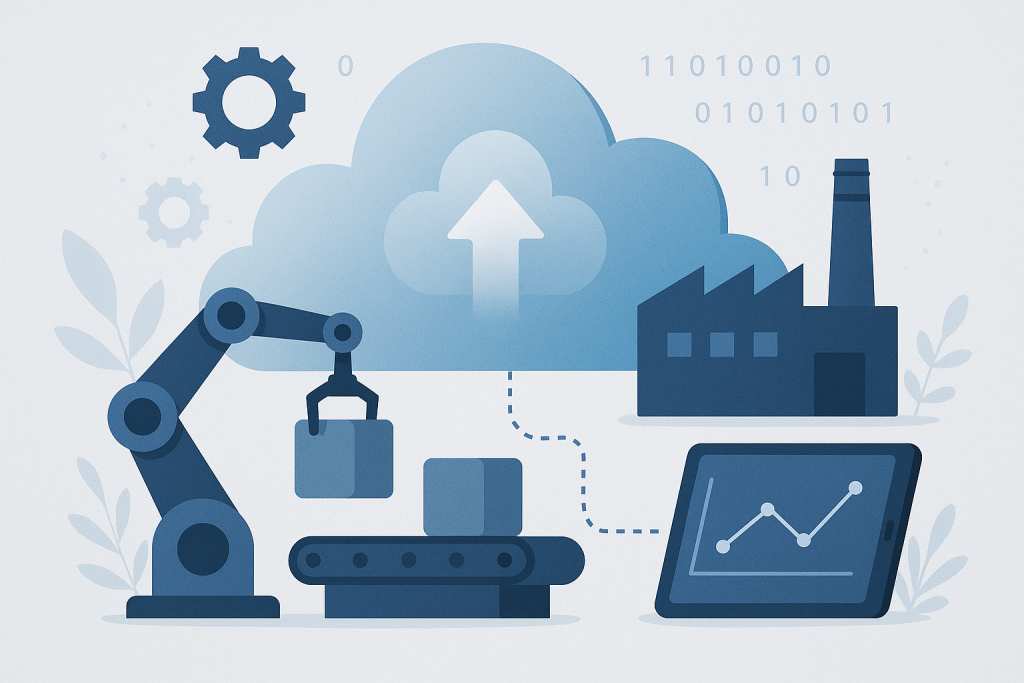
Cloud computing has revolutionized many industries, bringing flexibility, scalability, and cost-effectiveness to the forefront. Yet, one sector has been slower to embrace this shift — manufacturing. The hesitation is not because manufacturers do not understand the benefits, but because they still rely heavily on real-time systems, old equipment, and managing everything on-site.
But times are changing. As Industry 4.0 continues to gather momentum, cloud migration is no longer just an option for manufacturers — it is quickly becoming a key enabler of agility, predictive maintenance, and smarter, data-driven production.
In this blog, we explore what happens when real-time systems meet the cloud. We will look at the unique challenges manufacturing faces in this transition, and how businesses can successfully navigate them to unlock the full potential of digital transformation.
The Unique Nature of Real-Time Systems in Manufacturing
Manufacturing environments function under the tight constraints of timing and accuracy. A single delay in data transmission or control signals can potentially interfere with production lines, result in defects, or cause significant downtime. Real-time systems are responsible for:
- Machine automation and control
- Quality monitoring and evaluation
- Predictive analysis for maintenance.
- Tracking inventory and logistics
- Safety and compliance systems
These systems generally run on Programmable Logic Controllers (PLCs), Supervisory Control and Data Acquisition (SCADA) systems, and Distributed Control Systems (DCS)—all originally designed for low latency and local processing. These setups prioritize uptime and response time over connectivity or cloud integration, so migrating them to a cloud environment is more than mere duplication—it is an entire rearchitecture.
Cloud migration thus raises a very relevant question: Can reliable real-time industrial systems be possible when their intelligence has a cloud foundation?
Why Manufacturers are Now Eyeing the Cloud
Despite some concerns, more and more manufacturers are turning to the cloud — and for good reason. The benefits are becoming too valuable to ignore:
1. Bringing Data Together Across Locations
With cloud platforms, manufacturers can finally break down data silos. Centralized dashboards give teams a clear view of what’s happening across different factories, helping them spot trends, improve forecasts, and benchmark performance. It is easier to find what’s working, fix what’s not, and make smarter decisions, faster.
2. Scalable Compute Power
Enables top-tier applications such as machine learning, AI quality inspection, and digital twin simulation to simulate production environments without compromising live operations..
3. Running Things from Anywhere
Enables remote visibility and control, particularly after the pandemic, enabling companies to keep operations running with reduced on-site staff.
4. Cutting Down on Infrastructure Costs
Moving to the cloud means less dependence on expensive, energy-hungry hardware. It also eases the load on in-house IT teams, freeing them up to focus on strategic work instead of constant maintenance.
5. Faster Innovation
Allows rapid prototyping and deployment of new production models, tools, and services without disrupting core manufacturing operations.
Key Challenges in Cloud Migration for Manufacturers
- Latency and Real-Time Responsiveness: Cloud networks could introduce intolerable latencies unacceptable for mission-critical workflows. Delays of a few milliseconds would impact production quality.
- Old Systems, New Demands: A lot of factory equipment was never built to connect to the internet. Getting those legacy systems to work with the cloud can be tough. Sometimes it means retrofitting, other times it means full replacements — both of which can be costly and time-consuming.
- Security and Compliance: Cloud infrastructures must also adhere to stringent standards like ISO/IEC 27001, NIST, and industry-specific standards. Data sovereignty laws can also limit where data can be stored..
- Network Reliability: Limited connectivity at remote factory sites can be a significant bottleneck. Accordingly, manufacturers must make an investment in redundant and reliable network solutions.
- Cultural Resistance: Operational technology (OT) teams are often cautious about IT changes. Involving them early and showing real benefits makes all the difference.
The Solution: A Hybrid and Edge-First Approach
So, what’s the answer? It’s all about blending hybrid cloud architecture with edge computing. Here’s how it works:
- Edge Nodes take care of real-time data processing and control right on-site. Meanwhile,
- The Cloud steps in for data storage, analytics, orchestration, and providing insights across the entire system.
This setup guarantees real-time performance when it matters most, while still allowing for cloud-driven capabilities for tasks that aren’t as time-sensitive. Plus, edge computing serves as a safety net, keeping things running smoothly even during brief cloud outages or hiccups.
In fact, as manufacturing environments demand faster response times and local intelligence, it is becoming clear that edge computing is the future of cloud computing — especially in industries where every millisecond counts.
The Hybrid Cloud in Manufacturing Stack
Edge Layer: Closest to the machines — handles real-time controls, sensors, and PLCs. Speed and low latency are key here.
On-Prem Layer: Located within the factory — manages local storage, middleware, and system integrations. It connects the edge to the cloud without losing responsiveness.
Cloud Layer: Handles analytics, dashboards, and machine learning. Ideal for big-picture insights, remote access, and long-term planning.
Case Study: Cloud Migration at a Smart Automotive Plant
A German car manufacturer decided to take a hybrid approach. They kept real-time quality inspections on edge devices while shifting AI training to the cloud. This led to a 28% improvement in real-time defect detection, and cloud-based analytics helped cut downtime by 15%. Predictive maintenance also played a role in reducing costs.
To ensure a seamless integration of their legacy systems with modern cloud-native platforms, they utilized cloud migration services, all while preserving the integrity of their real-time operations. Additionally, the manufacturer rolled out digital twins to simulate new production processes, which significantly sped up the journey from design to market.
Real-Time Systems: Deployment Models Compared
Feature | On-Prem Only | Cloud Only | Hybrid Approach |
Latency | Very Low | Unreliable | Real-Time Capable |
Scalability | Limited | High | Flexible |
Cost Efficiency | High CapEx | OpEx Based | Balanced |
Security Control | Fully Owned | Shared Responsibility | Selective Isolation |
Innovation Speed | Slower | Fast | Fast |
Cloud Across Industries
- Pharma: Cloud-based dashboards that help track compliance in real-time
- Aerospace: Predictive maintenance for high-value assembly lines
- FMCG: AI-powered detection of packaging defects, all managed in the cloud
- Textile: Monitoring yarn tension in real-time with edge-cloud hybrid models
- Electronics: Quick anomaly detection through sensor fusion in cloud analytics
These examples from various sectors highlight the wide range of applications and demonstrate how even specialized manufacturing processes can gain from cloud technology.
Conclusion
Cloud migration in the manufacturing sector goes beyond a simple tech upgrade — it represents a strategic transformation. When real-time systems integrate with the cloud, they usher in a new age of visibility, agility, and intelligence. The trick is to design architectures that harmonize edge processing with cloud capabilities, allowing for real-time control while sparking innovation.
Manufacturers who master this balance will spearhead the movement into Industry 5.0, where humans, machines, and the cloud work together seamlessly. By tapping into the right cloud migration services and establishing an infrastructure that meets real-time demands, manufacturers can transition smoothly without losing control or precision.
The moment to rethink your factory floor’s potential is now — not just in terms of output, but also in agility, resilience, and intelligence. Cloud migration is not a future concept; it’s today’s most strategic choice.